


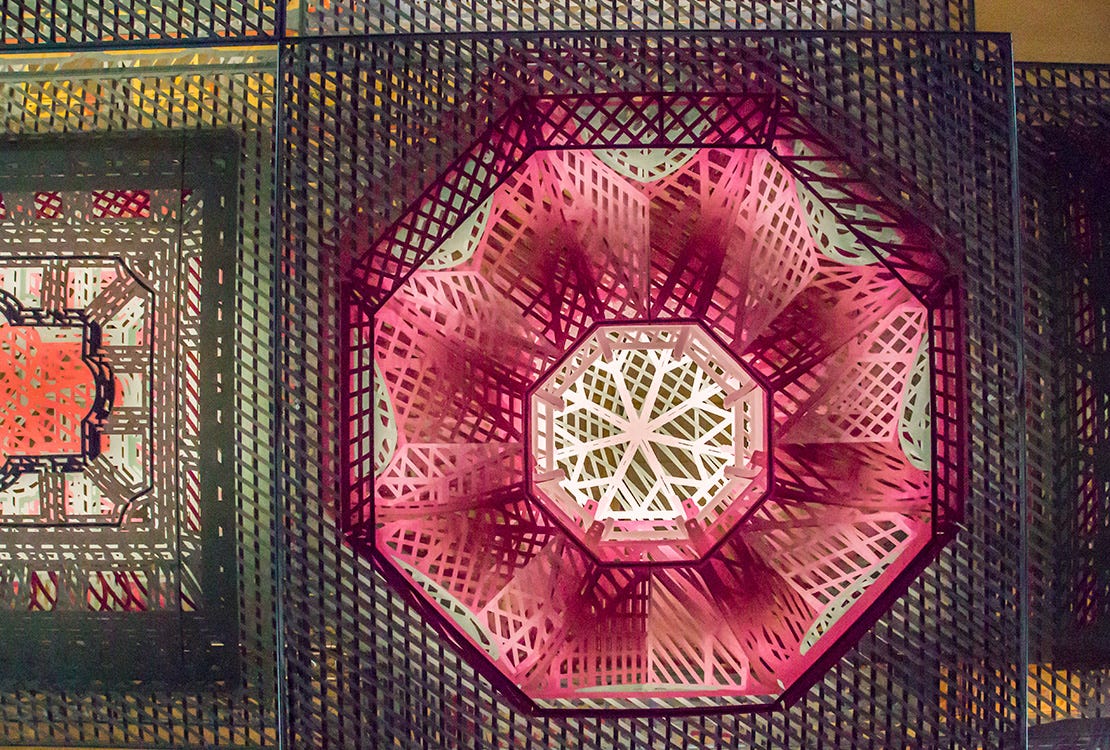




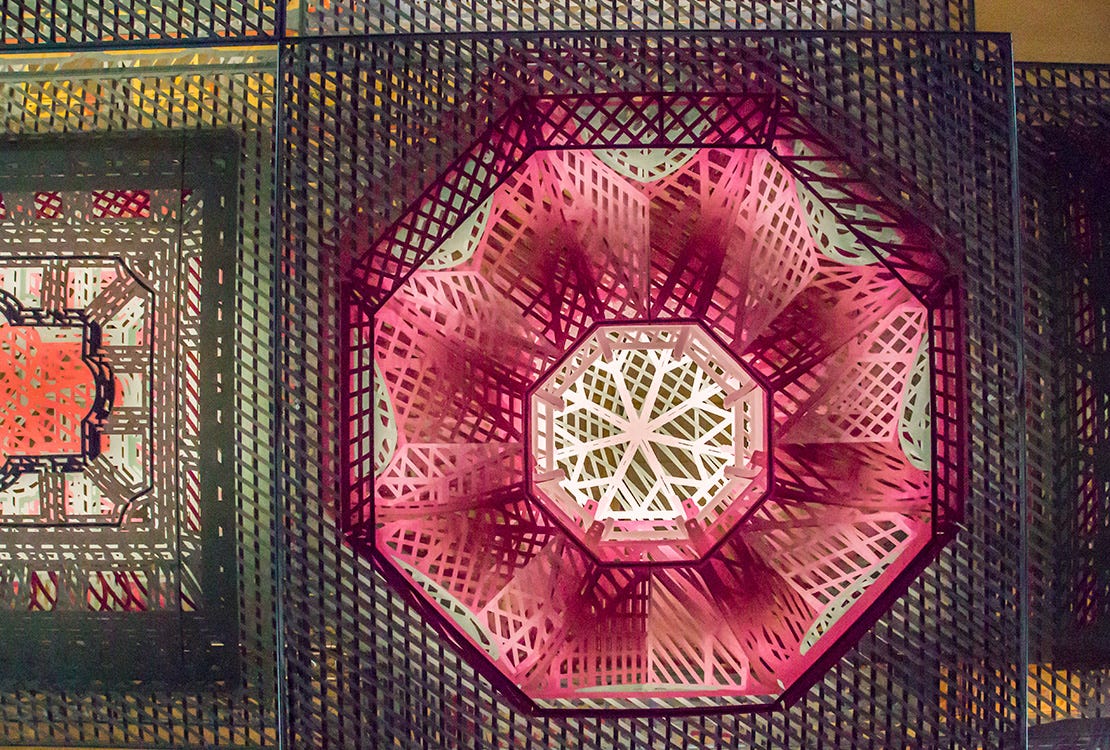

Client | FreelandBuck / Smithsonian |
---|---|
Design by | FreelandBuck |
Engineer | NOUS Engineering |
Download Case Study PDF
Fabric Images® partnered with FreelandBuck to bring life to Parallax Gap, an 83ft x 38ft suspended ceiling structure that interprets the line drawings of nine iconic American ceilings from the 19th and 20th centuries through six over-lapping layers. Parallax Gap was installed at Renwick Gallery’s Grand Salon within the Smithsonian for eight months.
Fabric Images manufactured the canopy and played a crucial role in developing the fabrication technique. As stated by Brennan Buck, partner with FreelandBuck, “Fabric Images was willing to work with us over a number of years on several speculative projects while we developed the material and design strategies to execute Parallax Gap… Fabric Images is open to experimentation and multiple ways of executing a project, but they also have the expertise and proprietary products and materials to produce very high-quality results.”
Fabric selection for Parallax Gap accounted for the following:
- The fabric would have to maintain its shape with 50% of the material removed.
- The fabric, once cut, could not unravel or curl along the edges.
- The fabric had to be polyester-based and printable using the dye-sublimation print process.
- The fabric had to meet fire codes for the installation site.
- The fabric required strength and rigidity to support strategically placed LED tape lights at opening areas.
- The fabric had to be available within the short timeframe required for completion.
These requirements led to a 10-foot-wide industrial-grade non-woven polyester. The project required five hundred yds of material.
Using Rhinoceros and Grasshopper software, drawings were created for each layer to achieve cut patterns that represented the three-dimensional line drawings. Once the files were aligned, the fabric was CNC cut, making the latticed pattern representing the isolated lines, hatches, and curves.
After the fabric was printed and cut, a silicone membrane was sewn along the perimeter and inserted within a proprietary extrusion frame with a powder-coated finish. Each layer was suspended, one from the next, for a total overall height of around 8 feet. The minimal and clean finishing application supported the fine detail of the design. Precise manufacturing led to a three-dimensional representation that visually changes based on the perspective from below.
